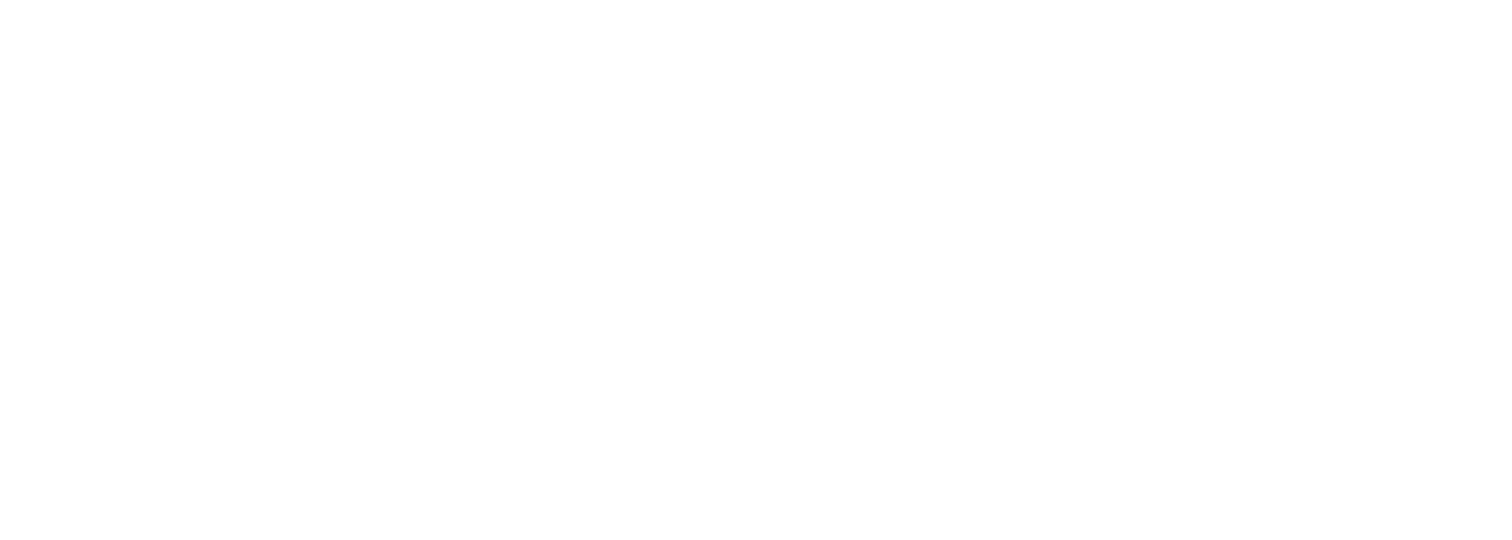
「生きるための欲求」を引き出す
デジタルファブリケーション
データから直接、造形物を生成するデジタルファブリケーション。田中浩也氏は、早くから3Dプリンターに着目し、その活用方法を探ってきました。現在注目するのが、その「潜在的な欲求を引き出すメディア」としての可能性です。果たしてその意図するところは? 数多くの具体例を挙げながら、説明していただきました。
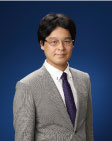
慶應義塾大学環境情報学部教授。京都大学総合人間学部卒業、東京大学大学院工学系研究科修了、博士(工学)。2012年マサチューセッツ工科大学建築学科客員研究員。慶應義塾大学SFC 研究所所長。専門はデジタルファブリケーション。3Dプリンターを駆使して、その可能性を探究する。
「1人1台3Dプリンター」の環境が
生み出すもの
—早くから3Dプリンターを活用していると伺いました。
田中:そうですね。おそらく、日本で初めて自宅で3Dプリンターを使い始めた人間だと思います(笑)。
—「デジタルファブリケーション」とは何ですか?
田中:デジタルファブリケーションの特徴は、マテリアルとデジタルデータを組み合わせることで、新しい何かを“直接”生み出せる点です。この“直接”というところが重要なんです。現在、大抵の工業製品は、デジタルCADデータなどから作られていますが、中間に金型などが必要になります。その点デジタルファブリケーションは、データから直接、製造物が生み出されます。そのデバイスは、3Dプリンター以外にも、レーザーカッターやデジタルミシン、CNC加工機といった装置があります。
—その中で、最も可能性を感じたのが3Dプリンターというわけですね。
田中:ええ。ゴミが出ない、騒音も出ない、そして安全であるという3つの要素がそろっていて、家庭に導入しやすく、女性や高齢者でも扱いやすいんです。大学の研究室でも以前から「1人1台3Dプリンター」という環境を作りたいと考えていました。1人1台パソコンといった状況と同じです。価格がだいぶ手頃になったということもあり、実際に今の研究室の学生は、全員3Dプリンターを持っています。
—学生たちは、どのようなものを出力しているのですか?
田中:本当に多種多様です。変わったところではチョコレートをマテリアルに選んで出力している学生もいますね。何を作るかアウト・オブ・コントロールな状況です(笑)。普通は、もの作りを学ぶには、それぞれ専門の教育機関で学びます。食べ物だったら料理の学校、ファッションだったら服飾の学校。しかし私の研究室では、3Dプリンターがあるせいで、ジャンルにとらわれないクリエーションが発生しています。
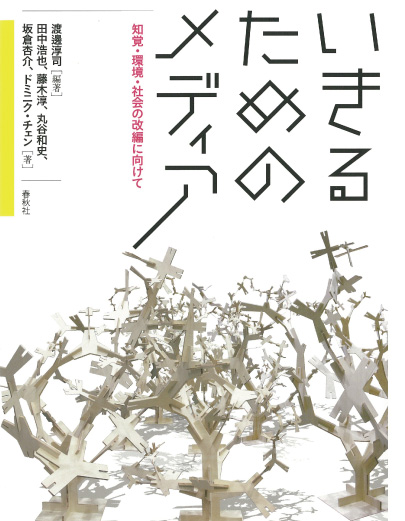
『いきるためのメディア -知覚・環境・社会の改編に向けて』
渡邊淳司、田中浩也、藤木淳、丸谷和史、坂倉杏介、ドミニク チェン/春秋社(2010)
田中氏は、2010年に本誌編集長(渡邊)と共著で単行本を執筆し、その中で「ソーシャル・ファブリケーションの近未来」について語っている。10年が経過して、その近未来が現在となり、そしてまた本誌で2020年からの近未来について語っていただく貴重な機会が得られた。
構造パターンによって
感触のバリエーションを生み出す
—3Dプリンターが活かせる分野は何でしょう?
田中:3Dプリンターは1個からものを作れる、しかもデジタルデータなので、サイズや形が自由に調整できるという特徴があります。例えば、靴のインソールのように体にフィットさせる必要のある製品などで、実用化が進んでいます。
—体にピッタリのものが作れるというわけですね。
田中:はい。メリットは、サイズや形のフレキシビリティだけではありません。3Dプリンターは、マテリアルを積層していくことで造形物を製作するため、内部構造を設計できるんです。つまり、構造パターンを変えることで、いろいろな硬さのものを作れるんですね。硬さのバリエーションは、これまでは素材を変えることで実現されていました。非常に手間がかかる方法です。しかし、3Dプリンターなら、構造を変えるだけで、さまざまな硬さのものをどんどん生成できるわけです。
—素材が同じで硬さの調整ができるのは画期的ですね。
田中:そうなんです。研究室では、いわばカタログのように、素材が同じで硬さの異なるものをラインナップしています。私たちはこういった素材を「メタマテリアル」と呼んでいます。自然にはなかった物性を備えた素材ということですね
さまざまな感触を持つメタマテリアル構造の素材。例えば、スポンジやゴム、牛肉といった既存の材質はもちろん、従来の材料にはない独自の硬さ・柔らかさを任意に作り出すことも可能になる。義足や義肩など、人間の身体に快適にフィットする製品には、部分に応じて硬さ・柔らかさを自在に作り出せるメタマテリアル技術が威力を発揮する。
構造で硬さをコントロールできるということは、実は環境面でも大きなアドバンテージがあります。例えば、部分によって硬さの異なるものを作るには、従来は複数の素材を組み合わせる必要がありました。しかし、3Dプリンターであれば構造によって硬さを変えられるので、1種類の素材で作れるわけです。従って廃棄する際の分別が不要で、リサイクル性も非常に高いといえます。
構造パターンを変更し、硬さの異なるメタマテリアルを分布させたインソール。3Dプリンターを使うことで、硬さと形状を自由に設定できる。
トライ&エラーを短期間で実現して
「生きるための欲求」を引き出す装置
田中:3Dプリンターは社会の問題解決にも活かされています。例えば、義手や義足といった装具(ハーネス)の製作です。この分野での活用には、かなりの手応えを感じています。デジタルデータ上で修正して出力すればいいので、形やサイズの微妙な調整が、従来の方法に比べて非常に容易なのです。
—具体的な事例を教えてください。
田中:右肩が欠損している女性の方のための「義肩」を作っています。その方はもともと一般的な義肩を利用していたのですが、服を着たときの左右のバランスが気になっていたそうなんです。つまり審美的な不満が出発点でした。ところが、審美的な欲求が満たされたあとも、やり取りが続いたんですね。特に3Dプリンターの仕組みを理解してもらったあとには、「こんなこともできませんか?」といった具合に、さまざまなリクエストをいただきました。
—新しい欲求が引き出されたということでしょうか?
田中:そうですね。もちろん作っているわれわれもやりがいを感じていたので、その欲求に応え、何度もやり取りを続けていきました。すると最終的には、リュックを固定できるような穴を義肩に付けるというリクエストをもらったんです。もはや「機能を補完するための装具」ではなく「付加価値が加味された道具」です。3Dプリンターのようなデジタルファブリケーションだからこそ引き出せたリクエストだと思います。
—欲求を引き出しながらデザインを進めるというプロセスが興味深いですね。
田中:言い換えれば、それは、いつの間にか抑圧されていた欲求なのかもしれません。また、毎週のようにやり取りをしていると、使用者もファブリケーションに参加しているような気持ちになってくるんです。すると、プロダクトに対して、より愛着を持つようになってくる。いわゆるユーザーエンゲージメントが生まれてくるんですね。
—ほかに同様のケースはありますか?
田中:中学2年生の女の子のための義足を作ったことがあるのですが、そのときのリクエストはヒールの付いた靴が履きたいというものでした。普通の義足は安定性を重視するので足首に角度が付けられず、高いヒールの靴を履くことができないんです。3Dプリンターでヒールが履ける義足を製作したところ、とても喜んでくれました。
ただ、その出来事がテレビで報道されたので、翌日から研究室に問い合わせが殺到したんです。すべて「こんな義足を作ってほしい」という内容でした。中には、サーフボードと一体化した義足が欲しいというサーファーの方や、義足で雪駄を履きたいという男性の方もいましたね。いずれもデジタルファブリケーションが喚起した欲求といえます。「義足の方は、今まで靴を選べなかったんだ」ということに、あらためて気付かされました。
未来を生きるための
デジタルファブリケーションの意義
—顕在化していない欲求は、障がい者の方に限らず、誰でも持っていることのように思います。
田中:そうですね。そういった欲求を引き出す力は、特に日本がすでに迎えつつある超高齢化社会においても重要です。デジタルファブリケーションによる装具の製作は、非常に貴重な研究となりました。
私は学生時代に、河合隼雄先生の下で箱庭療法を学んでいたことがあります。そこでわかったのは「人間の心の中は外に出してみないとわからない。でも、何もない状況で出すことは難しいので、ある程度準備されたもの、つまりメディアのようなものが必要だ」ということです。
—そのメディアが、箱庭だったりデジタルファブリケーションだったりするというわけですね。
田中:はい。日本でのデジタルファブリケーションの始まりは、メイカームーブメントでした。そのベースにあるのは、アメリカのDIYカルチャーですが、日本にはちょっと合わない部分もあったように思います。では、日本ならではのデジタルファブリケーションとは何か? そういう疑問を前から持っていたんですね。“メディアとしてのデジタルファブリケーション”という考え方は、その疑問に対する1つの答えだと思います。
—これからの社会にとって、重要性がますます高まる技術ですね。最後に、今後の取組みについて教えてください。
田中:現在取り組んでいるテーマは「公園」です。今の公園は、画一化していてつまらない場所になっていると思うんです。また、触り心地や触感にもこだわっていません。そこで、デジタルファブリケーションで公園をアップデートできないかと考えたわけです。実はちょうど、30m 程度の造形物に対応した、大型の3Dプリンターを開発しながらプロジェクトを進めている最中です。
—30mというのは大きいですね。
田中:世界的に見ても最大級です。オリンピックイヤーに合わせて、その3Dプリンターを活用した公園を作ろうというプロジェクトです。具体的には「丘」を作ります。かくれんぼができるような丘です。子供だけでなく、高齢者も含めた多世代が集まる場所を想定しています。
高齢者にとって重要なのは、とにかく外に出ることだといわれています。そのための、行きたくなるような公園にしたいですね。丘だけではなく、座りたくなる材質のベンチなどもデジタルファブリケーションなら製作できます。今の時代に合うよう、公園をリデザインしていきたいと考えています。
生分解性の樹脂を材料に、大型の3Dプリンターを用いて作られたベンチやテーブルの例。
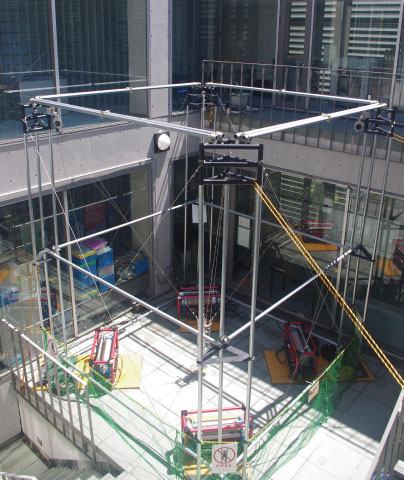
現在取り組んでいるのは3Dプリンターを活用した「公園」のアップデート。デジタルファブリケーションを駆使して、子供も高齢者も集まる場所を目指す。公園のベンチなど、最大30mの造形物に対応した超大型3Dプリンター「ArchiFab NIWA」も開発中。
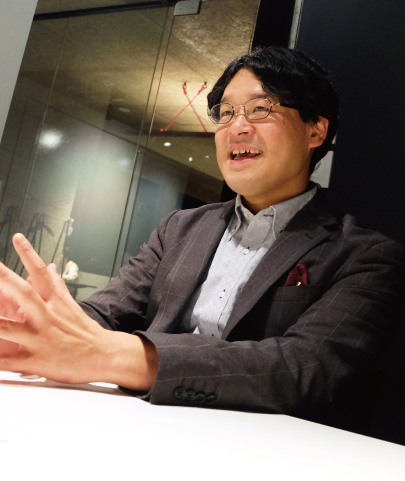
3Dプリンターを黎明期から導入し、その可能性を追究する田中浩也氏。大学の研究室で「1人1台3Dプリンター」の環境を整備したことで、デジタルファブリケーションの新しい試みが次々に生まれてきたという。